Design for Additive Manufacturing (DfAM): Maximize 3D Printing's Potential

This guide explores Additive Manufacturing and Design for Additive Manufacturing (DfAM) from overcoming their challenges to unlocking design freedom.
Introduction
Additive manufacturing (AM), more commonly known as 3D printing, is a transformative manufacturing technology that builds up three-dimensional objects from digital files.
As AM technologies continue to mature and their costs decline, 3D printing is seeing widespread adoption across many industries for rapid prototyping, low-volume and/or on-demand production, and customized manufacturing applications.
However, to fully leverage its design possibilities and maximize part performance, properties, and production cost-effectiveness, parts need to be designed specifically for additive manufacturing using the principles of design for additive manufacturing (DfAM).
Understanding Additive Manufacturing (AM)
There are several major differences between AM and traditional manufacturing methods.
Firstly, AM does not require expensive tooling like dies, molds, or fixtures to produce parts. This greatly reduces upfront capital costs for low- to medium-volume production.
Secondly, AM is a “bottom-up” process where parts are built one layer at a time from a digital design file, allowing for highly complex geometries that are impossible or inefficient to produce otherwise.
Lastly, AM offers unprecedented design freedom and functional integration, enabling lightweight topology optimized structures and even moving parts.
Major industries that are seeing huge benefits from AM include aerospace, industrial equipment, consumer products, dental and medical implants.
AM also enables mass customization through on-demand spare part manufacturing. The medical device industry utilizes 3D printing to create customized implants, orthosis and surgical guides based on patient scans. Overall, AM technologies continue to transform design and manufacturing across many sectors.
The Significance of Design for AM (DfAM)
Design for Additive Manufacturing, also known as DfAM, refers to the practice of designing products specifically for 3D printing processes. DfAM requires considering how a part will be additively manufactured during the design phase to take full advantage of AM capabilities:
Product designs can be optimized for AM, resulting in stronger, lighter, and higher-performing parts.
Complex assemblies can be consolidated into single components. This simplifies production and assembly and has cost-saving implications.
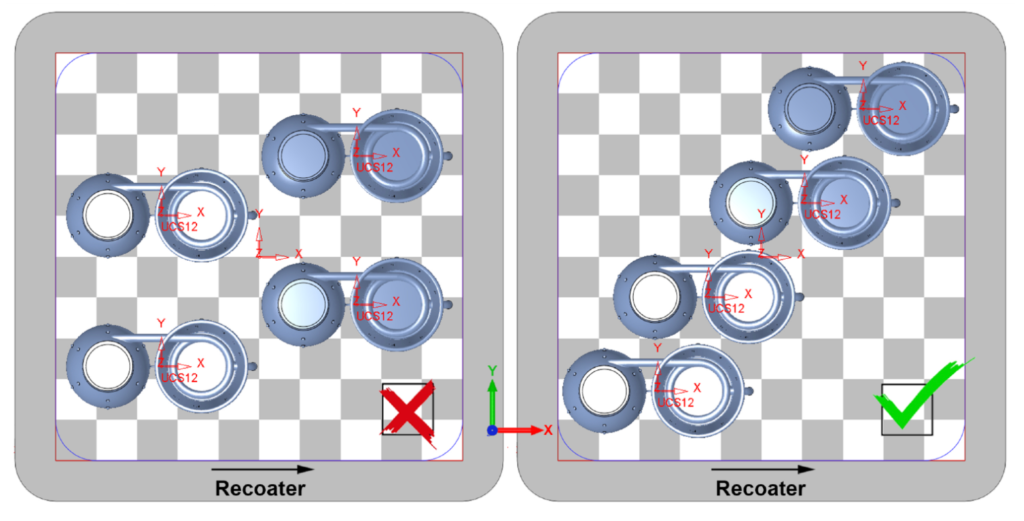
Source: metal-am.com.
Support structures, recoating patterns, and build directions can be optimized to minimize material usage and print times.
Intelligent design of internal features like conformal cooling channels can improve functionality. This enhances process control and reliability for applications like molds and dies.
Upfront planning allows for easier post-processing and avoids ill-suited designs that require substantial post-AM machining or rework.
Key Principles of DfAM
Design Simplicity
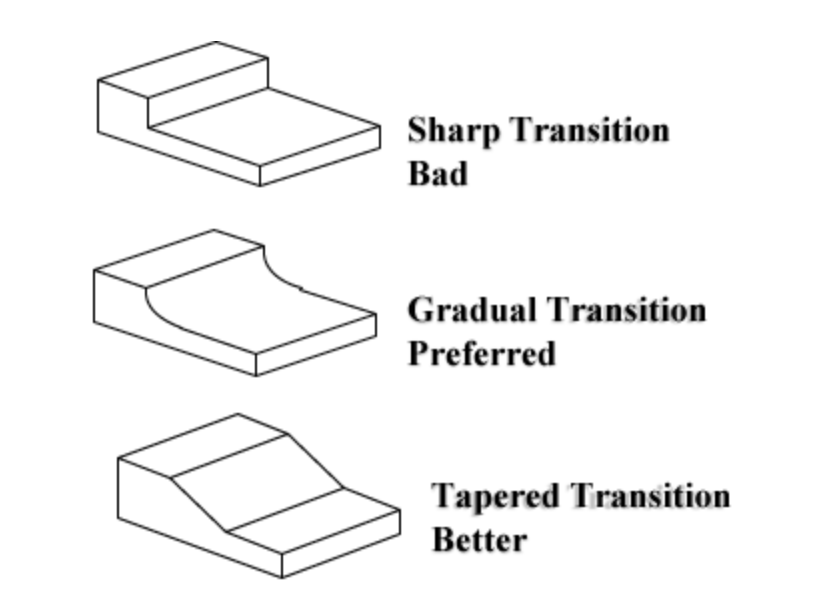
Avoid thin walls, narrow channels and small intricate features that may be difficult to print with appropriate resolution and accuracy. Thicker cross-sections are better. Create designs with tapered transitions between thick and thin walls. This prevents warping issues.
Keep internal cavities, holes and undercuts large and space them sufficiently apart. Narrow passages can trap uncured resin or powder.
Minimize overhanging geometries that require support structures. Supports introduce surfaces that need post-processing work.
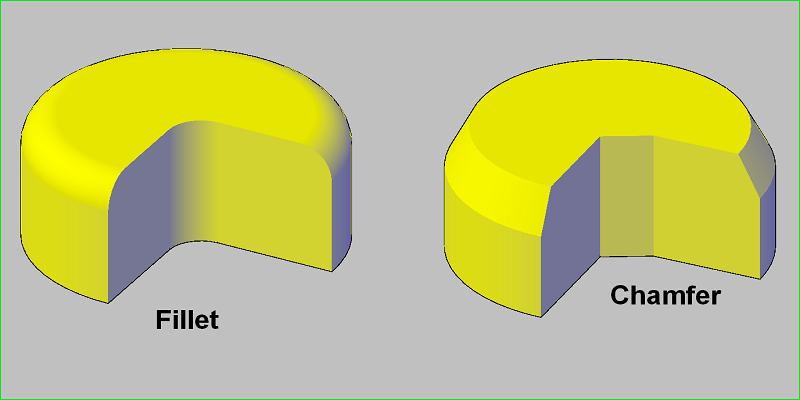
Fillet: rounded corner, good for load-bearing.
Chamfer: angled edge, better for assembly.
Use fillets and rounded edges where possible instead of sharp corners and angles. They have better printing performance.
Employ a Minimum Feature Size rule - don’t model any components/holes smaller than the AM system’s achievable resolution.
Simplify complex surface textures and finish. AM has limitations in replicating very fine intricate textures achievable with other processes.
Topology Optimization
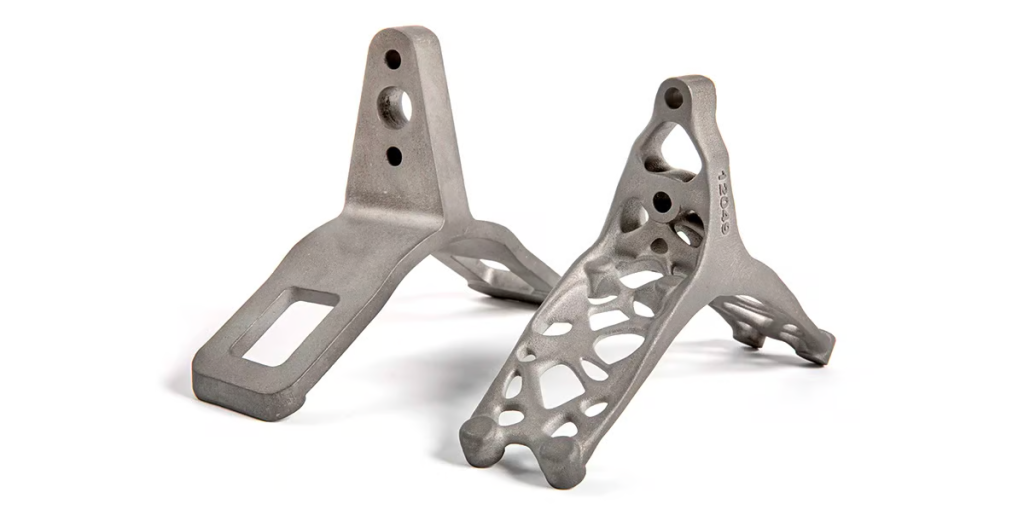
Topology optimization involves using simulation software to rearrange material within a given design space in order to create lighter structures that perform just as well mechanically.
The software removes unnecessary material while maintaining critical load paths, leaving minimal mass distributed optimally for strength.
Common topology optimization goals include minimum weight, compliance (stiffness) or stress objectives to determine efficient load-bearing shapes.
This technique is highly beneficial for AM since printing optimized lattices and hollow geometries is possible without many machining constraints. Both engineers and algorithms have more design freedom since AM doesn’t require simple x-y planar fabrication.
Part Consolidation Through Monolithic Design
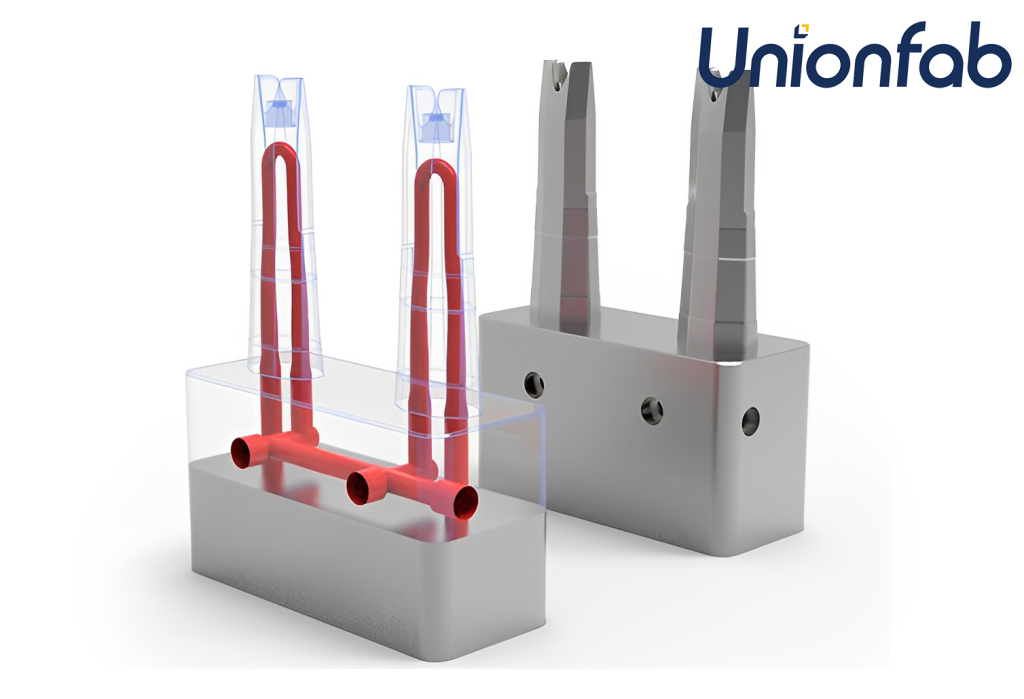
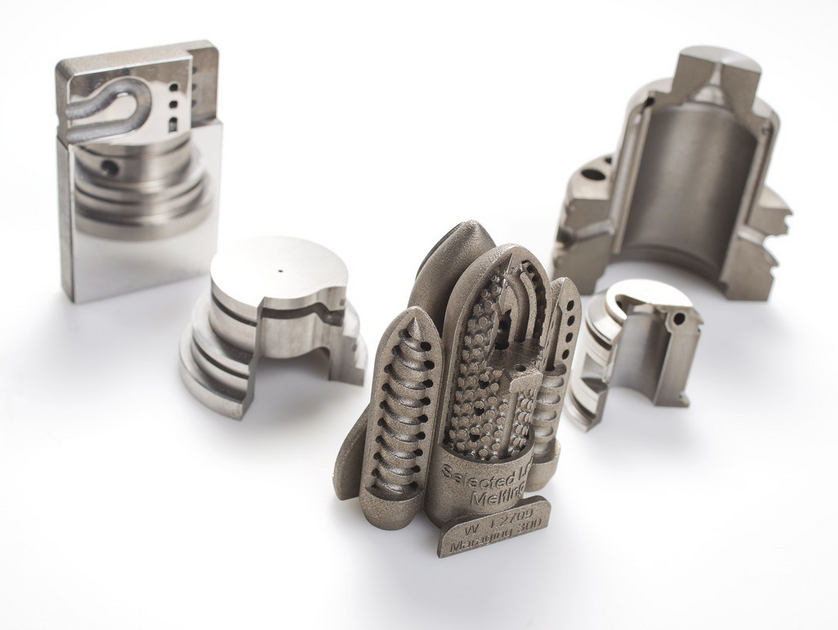
Engineers identify adjoining components that would traditionally be separate pieces and merge them organically within the model. Complex internal structures and pathways can be included that would be impossible to manufacture otherwise.
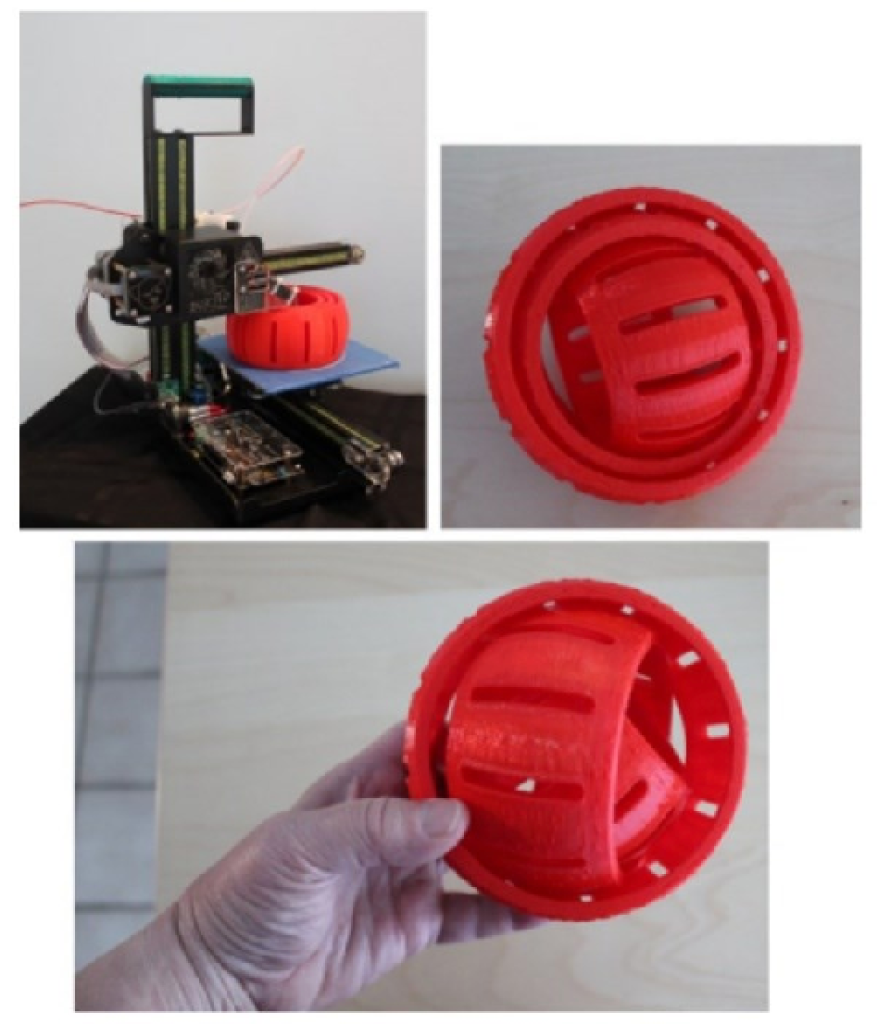
Moving assemblies need not have individual pieces joined; they can be integrated as the whole mechanism in one printing. Interfaces that were originally welds or fasteners simply become morphological transitions within the single body geometry.
Support structures are drastically reduced since overhanging geometries are eliminated by consolidating parts. Post-processing effort is minimized as well, because there are no joining steps and interfaces require no finishing work. Post-consolidation inspection and repair is simplified for a single-piece component versus an assembly of many.
Achieving Functional Integration
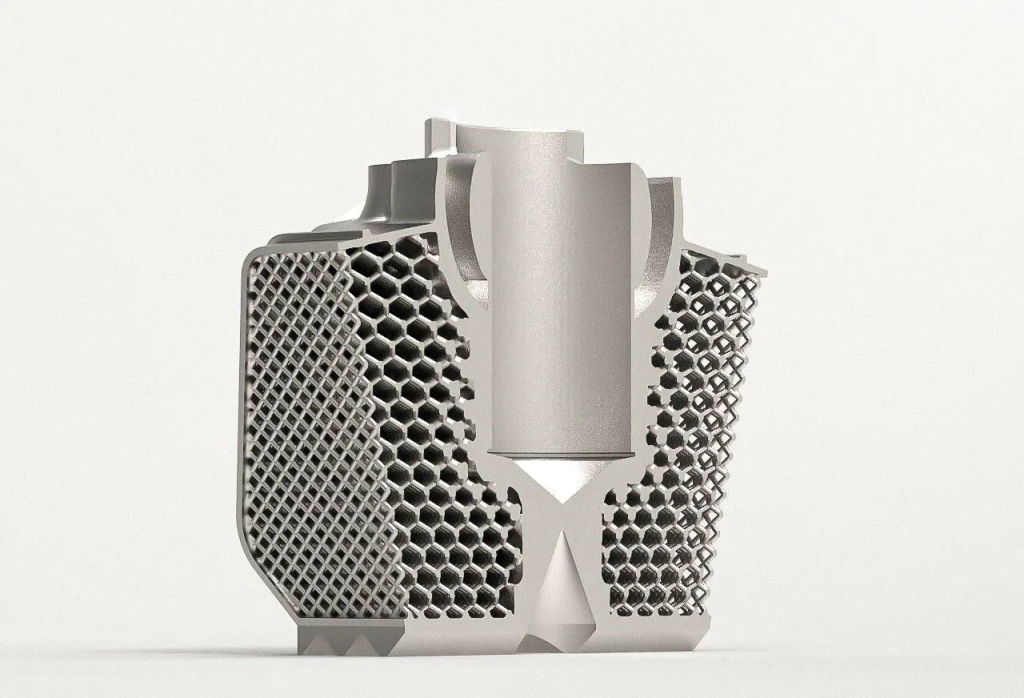
Embedded conduits: Design integrated channels/paths within parts for applications like conformal cooling inserts, fluid manifolds, turbine blades with enclosed piping. This improves thermal/fluid control.
Lattice structures: Optimized cellular designs can be applied to filter elements, heat exchangers, biomedical implants where permeability is critical. Integrates function of multiple individual pieces.
Integrated customization: Design modular parts with standardized interfaces that allow customized inserts/features to be added on demand through additional localized printing.
Conformal features: Curved geometries like anatomically matched prosthetics, ergonomic handles can be produced to precisely fit applications in ways not possible before.
Embedded electronics: PM techniques now allow for circuitry/wiring to be incorporated within 3D printed parts for applications like IoT sensors, smart prosthetics.
Post-processing in mind: Designs consider later processes like machining internal threads or attachment points to add functions mechanically.
DfAM Tools and Software
Generative Design Tools
Many DfAM tools leverage generative design algorithms, allowing designers to input parameters and constraints, and then autonomously generate numerous design iterations.
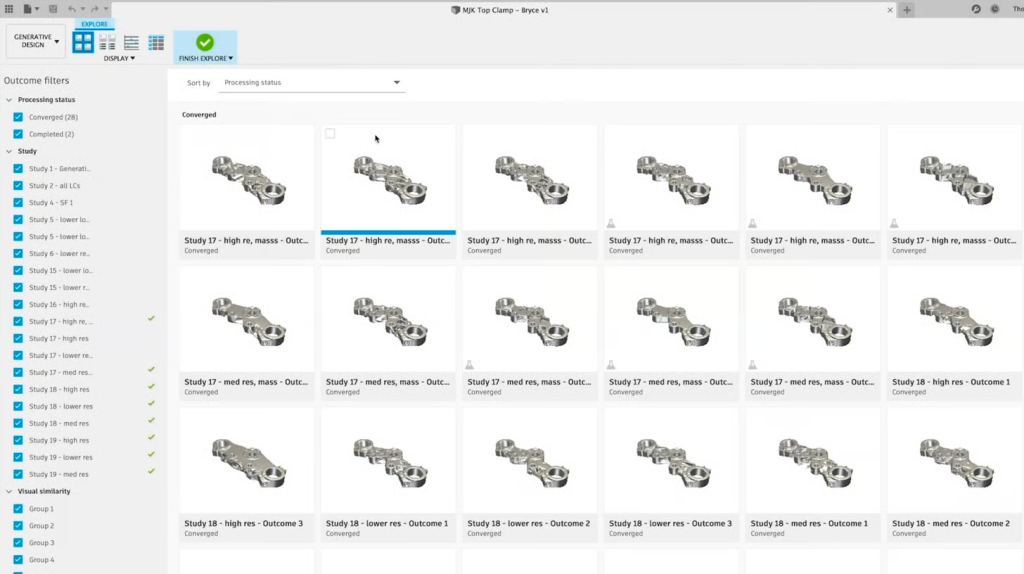
Autodesk Generative Design
Uses cloud-based generative design algorithms to explore numerous design iterations.
Integrates with Autodesk Fusion 360 for a seamless design workflow.
Altair Inspire:
Employs topology optimization to generate lightweight and structurally efficient designs.
Offers a user-friendly interface with real-time feedback on design changes.
Integrates with various CAD software for easy collaboration.
Topology Optimization Tools
Topology optimization software rearranges solid material into efficient geometric layouts according to load and boundary conditions. Programs can analyze a component and compute an optimized cellular structure design.
SIMULIA Tosca
A modular system that enables topology, sizing, shape, and bead optimization for mechanical structures.
seamless integration with prominent FEA & durability solvers such as Abaqus, Ansys, and MSC Nastran through Tosca.
OptiStruct by Altair
A powerful solver for structural optimization.
Enables topology optimization as well as shape and size optimization.
Known for its robust performance in handling complex optimization problems and is widely used in the aerospace and automotive industries.
Support Structure Tools
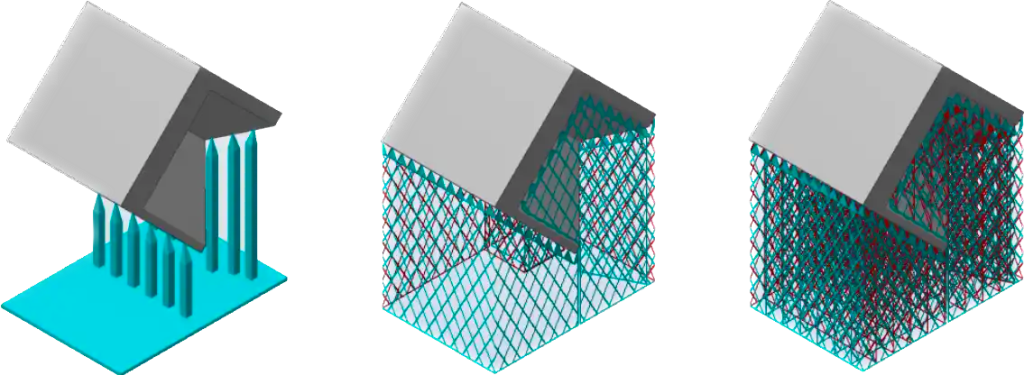
Source: Polydevs.
A comprehensive suite of tools for 3D printing model optimization, encompassing viewing, editing, repairing, orienting, and analysis.
Auto-generates and fine-tune support structures tailored to various types of geometries.
Smoother finishing process achieved with the creation of easily break-off contact points.
Ultimaker Cura
User-friendly interface for easy setup of support structures.
Compare factors like material use and print time for different orientations and support settings.
Tree support structures for efficient material usage.
Challenges and Limitations
There are some arguments that instead of delivering design freedom, DfAM imposed design restrictions, pushing engineers to work within the limitations of conventional AM systems. Well, it is true that AM is not without its certain challenges and limitations:
Material Properties
The ~material options for 3D printing~ are still limited compared to traditional manufacturing methods. Most metal alloys used in casting or machining are not available for additive manufacturing due to issues with printability, high temperatures, or porosity. This restricts high-strength, engineering-grade applications of DfAM. Research aims to develop more advanced metal powders and printing parameters to expand usable alloy materials.
Print Resolution
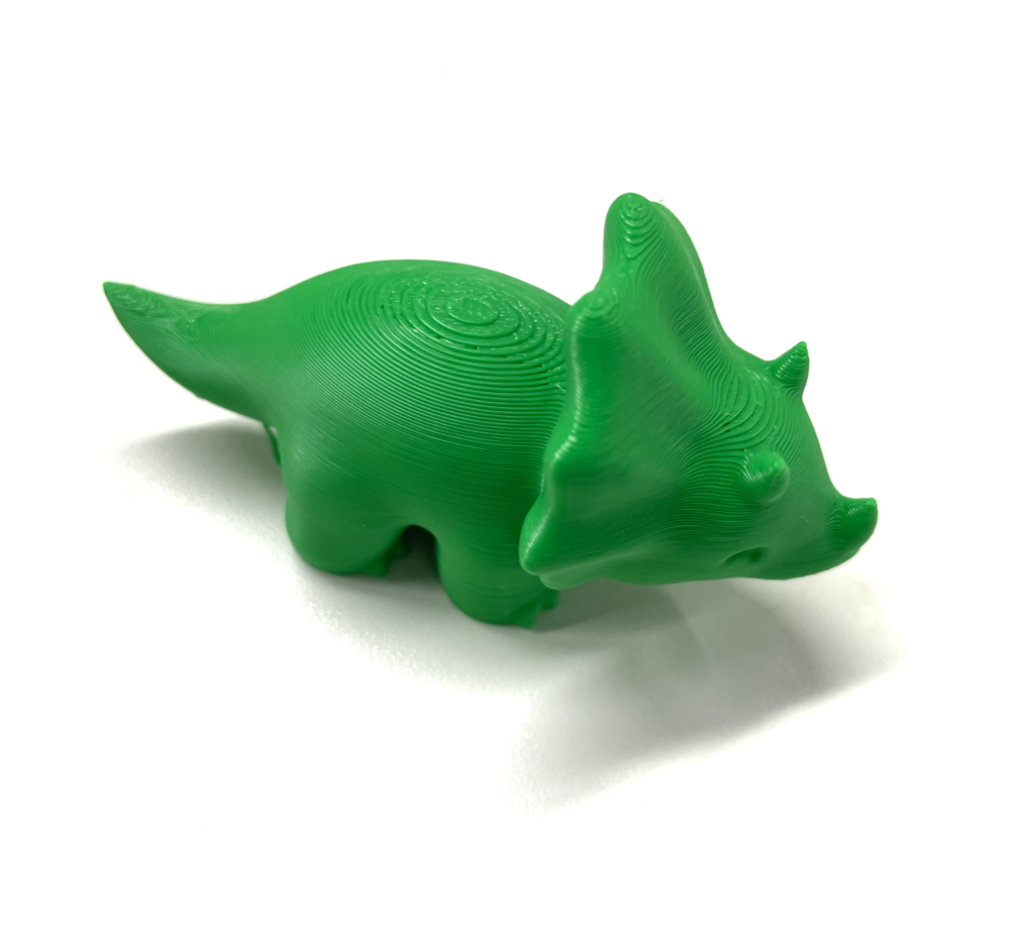
The layer thickness in 3D printing results in a stair-stepping effect on surfaces and limits geometric complexity. Finer resolutions are possible but substantially slow down build speeds.
Post-processing
3D printed parts often require post-processing like sanding, drilling, machining, or coating to achieve the desired finish. Minimizing these manual steps to reduce time and cost is a key research priority. Methods like integrated surface finishing are being explored.
High Cost
Both the additive manufacturing equipment and materials are currently high cost compared to traditional subtractive techniques. This prohibits cost-effective small-scale production. Work is ongoing to make machines and materials more affordable. Standardization of processes and parts commonality will also help drive costs down.
Companies like Unionfab are working to address this challenge through development of affordable, high-quality AM solutions. We have helped make 3D printing service accessible for small businesses and independent designers on a budget.
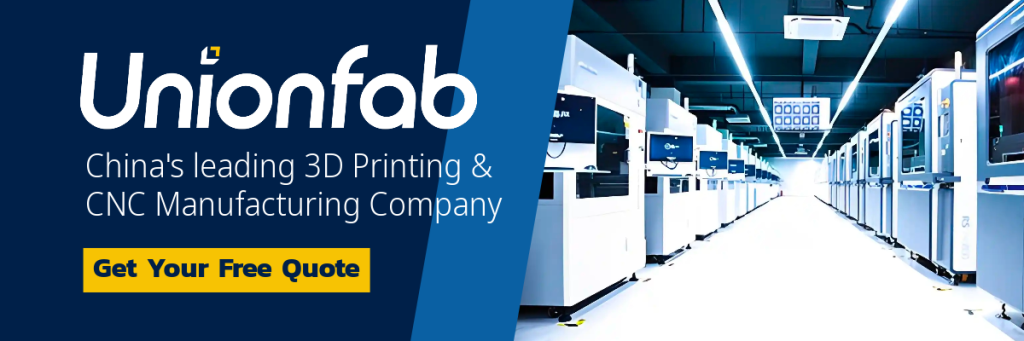
Conclusion
In summary, DfAM provides capabilities in complexity, customization, and optimization that are infeasible with subtractive techniques. The advantages have already been demonstrated in fields like aerospace, medical devices, and automotive.
While hurdles exist today, they are not fundamental limits. Continued ingenuity, research, and technological progress will further expand the potential of additive manufacturing and allow DfAM to profoundly impact how products are designed and made.